Swan Walk Car Park - Triflex (UK) Ltd
Project
Swan Walk Car Park
Product
Triflex DeckFloor with Emery
Size (M2)
4550m2
Contractor
Rateavon
Winner
LRWA Awards 2025 - Liquid Roofing Project of the Year
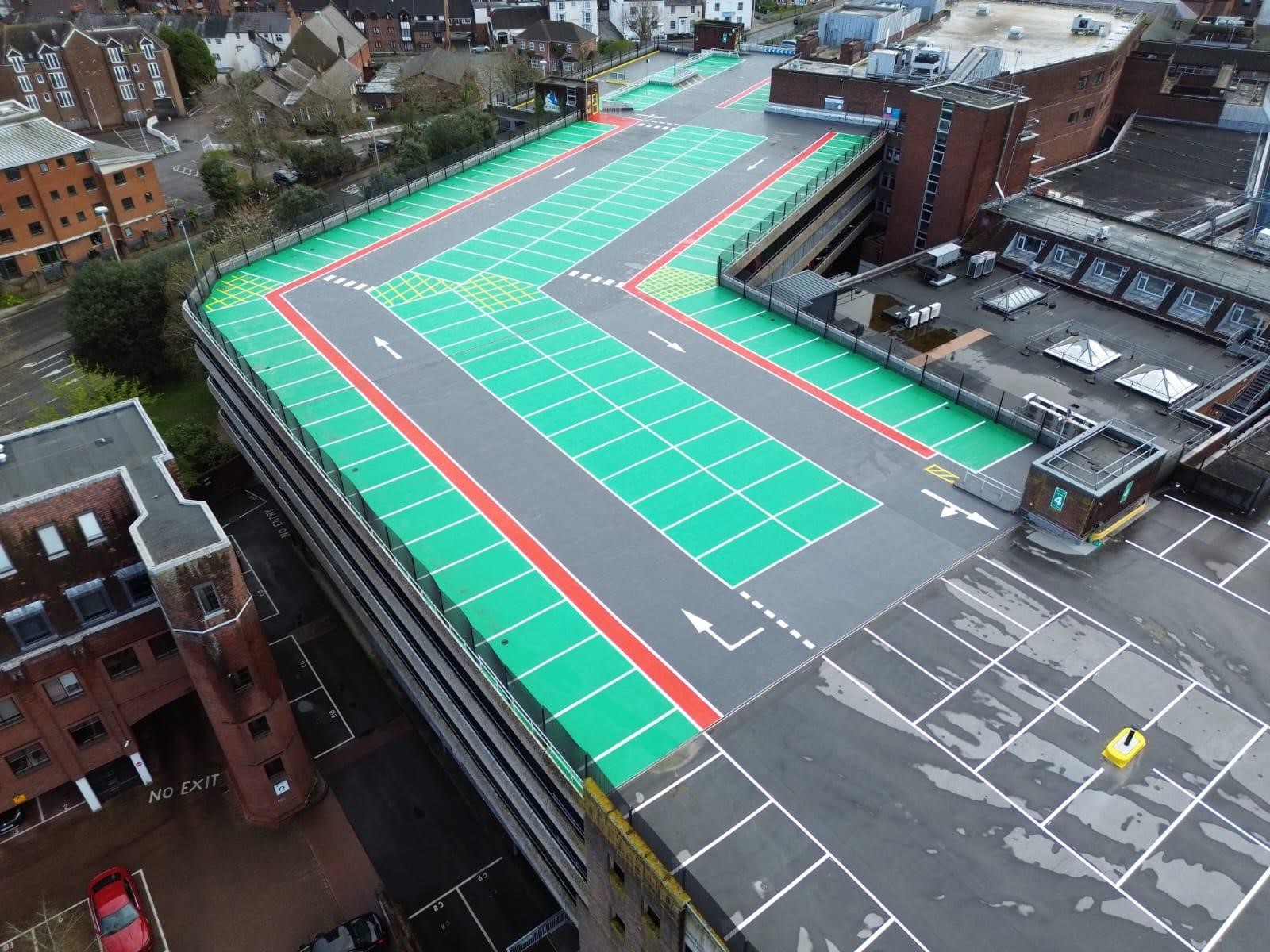
- The Background
The Swan Walk car park, a crucial 900-space facility supporting a popular shopping centre with 6.7 million annual visitors, recently underwent a major refurbishment led by Horsham District Council to ensure long-term structural protection and usability. Originally built in the 1970s, the car park’s top deck had been due for waterproofing and resurfacing work since 2019, but delays from budget limitations and the pandemic deferred a comprehensive repair. With funding secured the existing failed coating was removed, revealing extensive screed damage and water ingress.
The Triflex UK Ltd and Rateavon Ltd teams conducted detailed assessments, including adhesion and hammer tests, to fully characterise the whole surface and identify areas requiring replacement or repair. Triflex proposed their specialised DeckFloor with Emery aggregate, a robust, anti-skid waterproofing system, extensively used on ramps. Here it was innovatively used across the top deck to provide a durable, aesthetic surface to address the surface scoring from prior works by others. The Triflex, Rateavon, and Stripe Consulting teams successfully delivered a lasting waterproofing and protection solution, ensuring the car park remains functional and safeguarded for years to come
- The Challenge
Introduction
The 900 space Swan Walk car park serves a busy shopping centre in Horsham, estimated to have a footfall of 6.7 million a year. The car park is open 24 hours a day, 7 days a week and is the principal town centre parking location for the towns’ bars and restaurants too. Built in the 1970’s, owners and operators Horsham District Council required a waterproofing, surfacing and protection system for the external deck to ensure continued use and structural protection as part of their life care planning.
The previous deck coating system on the top deck of the car park was installed in 2008. With a life span warranty of 10 years, a life-care plan via Reportal® was implemented for the car park in 2018, with the top deck coating initially forecast for replacement in late 2019. The project involved removing the old membrane and replacing it to extend the deck’s durability and functionality.
However, due to budget restrictions and the eventual effects of the pandemic in 2020, a shorter term, lower cost approach was taken at this time to maintain the waterproof membrane and protect the structure below. This meant that patch repairs to the coating and underlying screed were carried out as and when required. Subsequently budget was granted in financial year 2023, and the existing system could be replaced.
A challenging substrate
Triflex UK Ltd and Rateavon Ltd joined the project at a stage where the existing failed coating had been removed from the top deck of the Swan Walk multi-storey car park, leaving the concrete screed exposed by others. The former appointed contractor had exited the project having uncovered the true extent of the project requirements in relation to the screed, and it was determined that it would be best to revert to Triflex as a specialist for the project.
Having previously surveyed the car park, the Triflex Technical team had identified the original coating as worn, delaminated and with numerous failures. Cracks had been noted through the existing coating in numerous places, and the underlying screed was also known to be in a poor state.
The now exposed top deck was resurveyed by the Triflex Technical team, working with Triflex Authorised contractor Rateavon Limited. The exposed screed was in poor condition, with water ingress evident under the screed. The substrate surface was also left deeply scored by the method the former contractor had used to remove the coating, adding to the challenge for resurfacing.
Methodical approach and condition mapping
The whole top deck required a methodical and analytical approach to assess the state of the screed, and determine the best approach to waterproofing, surfacing and protection. Conventionally an “easy” approach would have been to remove all the topping, and re-screed which would have a massive impact on both the length and cost of the project, with loss of revenue compounding losses. However, working together and with extensive knowledge the team developed an innovative approach to deliver the project outcomes effectively.
The Triflex Technical team carried out a series of adhesion and cohesive strength tests to determine a Triflex solution on this challenging and varied substrate. From the extensive tests undertaken it became clear that in mapping the condition across the whole area, that the screed was failing in multiple locations. The Triflex waterproofing systems adhere well to a range of substrates, and results showed good adhesion to the exposed screed. However, the surface of the screed failed indicating that in some areas the screed required replacement.
Taking up the challenge, Rateavon conducted a hammer test across the entire area of level 4. This 3 day in-depth study fully characterised the state of the screed and surface. This meant that areas of repair could be identified and catalogued. Failed screed areas were then cut out and replaced. These defective areas were repaired with a rapid curing concrete repair material. Rateavon also scratched out and infilled some of the larger gouges that were in the top of the screed to bring the standard of screed to and acceptable level of finish, ready to take the new Triflex waterproofing, surfacing and protection system.
Scarred surface countered with emery waterproofing solution
Mindful of the deep scoring and condition of the screed, Triflex proposed Triflex DeckFloor with Emery to create a robust surface that would help to level out the scarred surface. Triflex Deckfloor is a partially reinforced PMMA based system, certified to EN 1504-2 where reinforced, that has been developed for areas above parking. The system is cold applied and rapidly cures, even in low temperatures enabling the project to progress through the winter and early spring programme of works.
The incorporation of emery provided a tough anti-skid finish that is usually reserved for those areas with high forces such as ramps or heavy traffic. Here, the emery aggregate mix helped to level off the gouged surface across the whole of the external car park surface. This meant that the majority of the existing screed could be saved, rather than completely removed and re-screeded. The resulting surface is also aesthetically pleasing with a uniform appearance, combining a coloured finish for long lasting demarcation.
The Triflex, Rateavon and Stripe Consulting teams are highly experienced, and with their diligence and wealth of knowledge were able to provide a solution that could meet the needs of the difficult surface to deliver a waterproofing, surfacing solution that they are proud to put their name to, safe in the knowledge that the structure is protected for the long term.
- Gallery
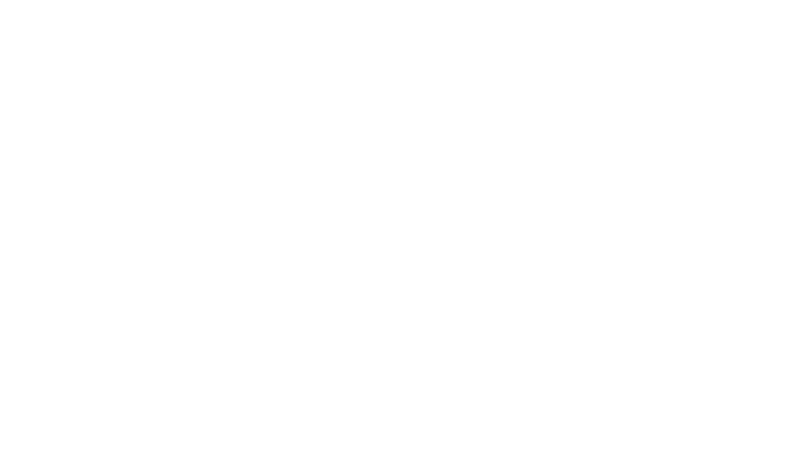
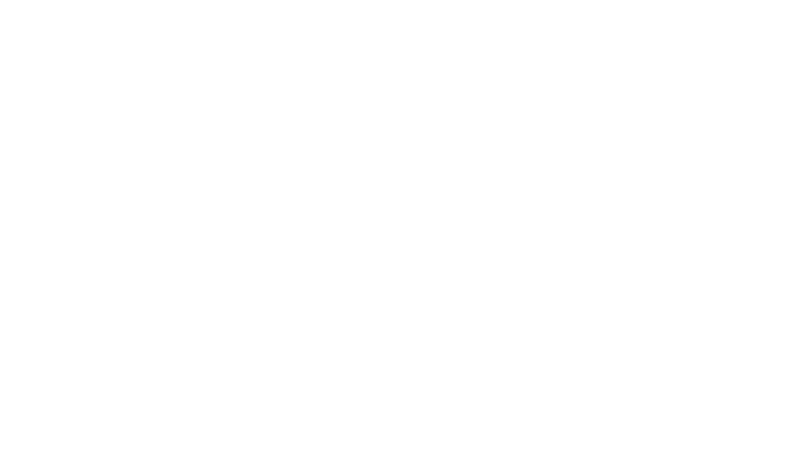
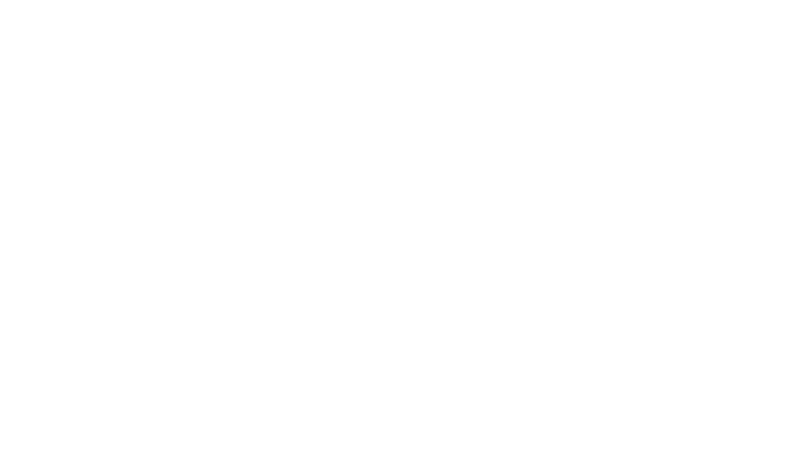
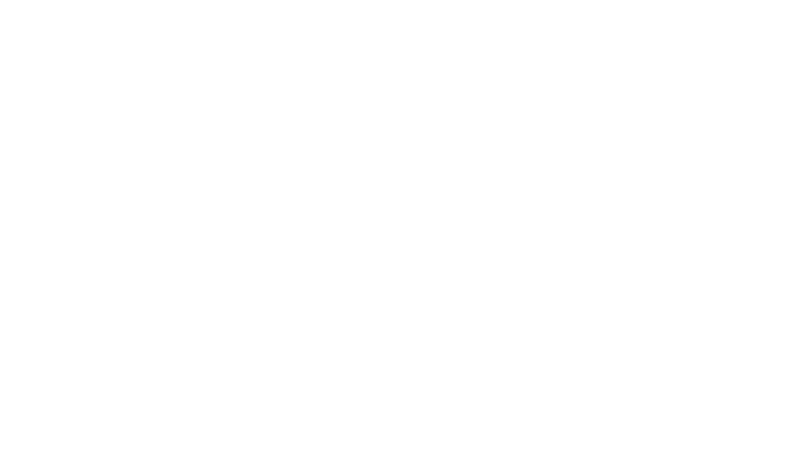
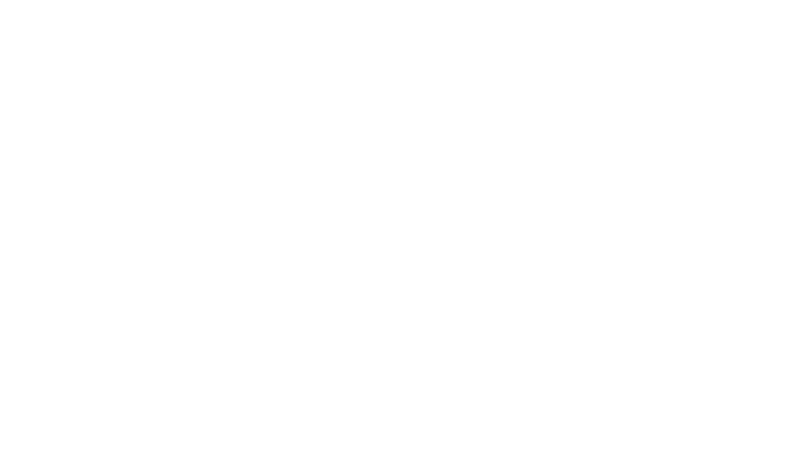