90 Long Acre - MAC Roofing & Contracting Limited
Project
90 Long Acre
Product
BMI Parabit & Sealoflex Ultima
Size (M2)
7000m2
Contractor
MAC Roofing & Contracting
Winner
LRWA Awards 2025 - Sustainability Project of the Year
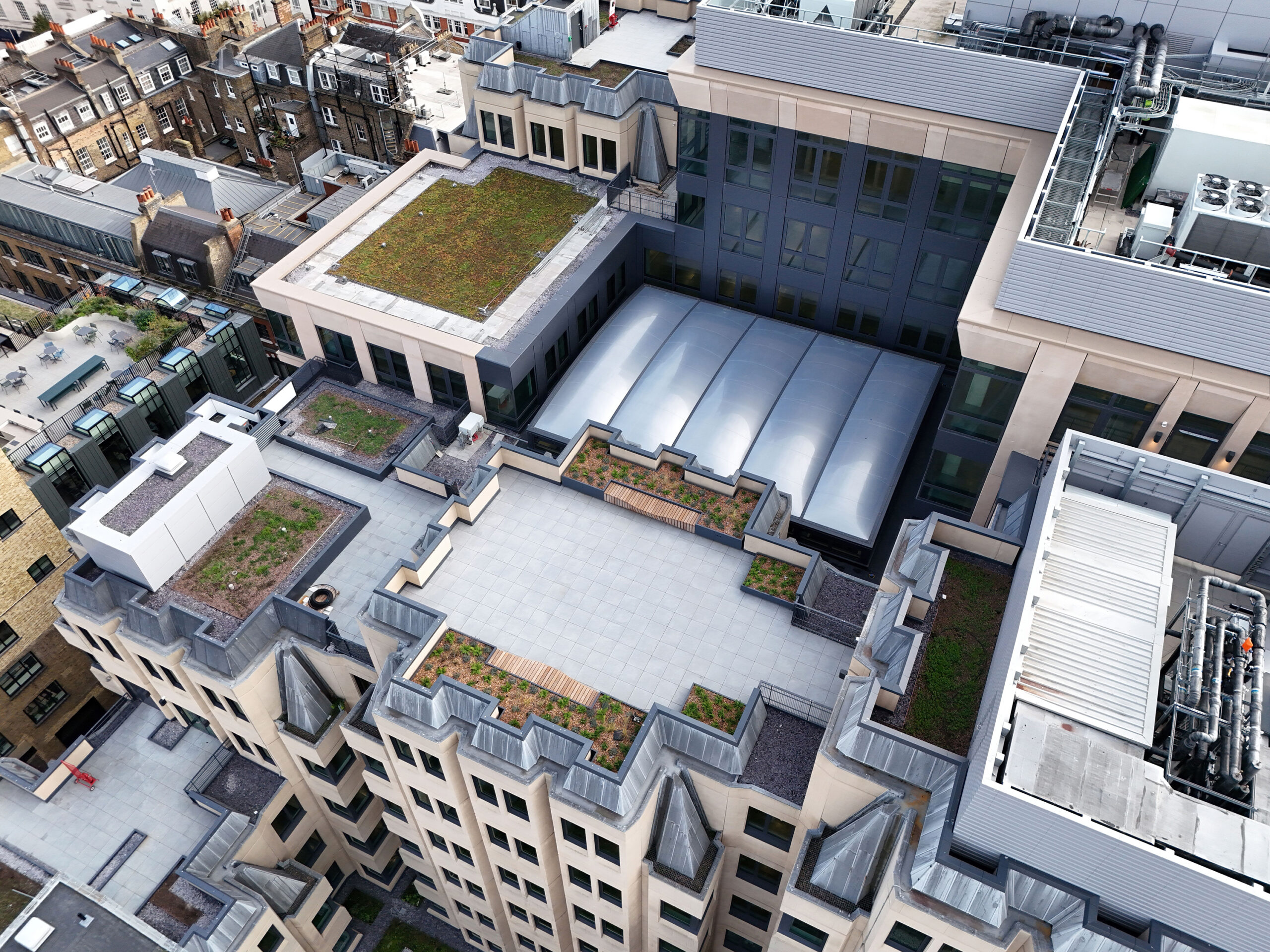
- The Background
Situated in the heart of Convent Garden, London, 90 Long Acre was originally built in 1981 and was called First Chicago House. In 2020 planning permission was granted to create Covent Garden’s largest office development with 240,000 sq ft of workspace and 20,000 sq ft of amenity and retail space.
During this project the building underwent extensive repositioning, with over 80% of the original structure retained. This was designed to reduce the embodied carbon by half compared with a full new-build proposal. The building was also specified to be net zero carbon in operation, thereby achieving top sustainability and wellness accreditations – BREEAM Outstanding, Nabers 4.5*, WELL Platinum and FITWEL 3*
- The Challenge
We are delighted to put this project forward as we believe it truly represents modern day construction when it comes to reducing environmental impact. For 90 Long Acre this has been achieved via the redevelopment and modernisation of an existing building in combination with a new build development (Cut & Carve*) which has reduced the embodied carbon by half compared with a full new-build development. From a waterproofing perspective, the roof areas were used to their fullest potential in order to contribute to the environmental performance of the building by incorporating both living/green roofs and a blue roof system.
In addition, this project demonstrated the use of multiple waterproofing systems being used in conjunction with each other to ensure maximum performance was reached for the client.
*Cut and Carve is the methodology used on construction & redevelopment projects where an element of an existing structure is retained as part of the construction.
Cut and Carve demolition is combined with temporary works to demolish a structure in a controlled way, to retain and modify the existing structure for its future use, which can include the additional floors.
The use of cut and carve by the construction industry has increased over recent years as planning, environmental and economic considerations increase the demand for the repurposing and reconstruction of existing structures.
Challenges
There were many challenges to overcome on this project, with the main challenges highlighted as follows:
1. Safety – The safety of our team and other individuals on and around site is our key target on any project. MAC are an ISO 45001 accredited company, and as part of our internal process we always carefully evaluate the risk of each project from design, installation and completion. To ensure that our teams were fully aware of their requirements on this project we conducted safe2start and safe2finish briefings each day, as well as conducting focused Toolbox Talks on key areas. HSEQ inspections were conducted on a regular basis by our HSEQ Team, with all HSEQ data measured against our own internal KPI minimum requirements.
2. Logistics – this project was located on a one-way street in a very busy part of London (Covent Garden), which is also a tourist attraction for many. This meant careful planning was required with both the main contractor’s logistics team and the other trades on site with regards to how we were going to bring our materials to site, how they would be lifted onto the roof levels and at what time. It was essential to ensure that all materials were safely secured on the roof, but it was equally important not to create congestion on the site or the surrounding roads which would cause disruption to the public. Collaborative planning was key because space on site was at a premium, and there were particularly tight delivery windows due to the number of other trades that were working on this project.
3. Design – This was not a straightforward project as the building was a mix of new build and refurbishment, where 80% of the current structure was to remain in order to reduce carbon impact of the project. However, this meant having to work with existing roof levels, threshold heights etc, and it also determined the weights of the systems that could be installed at each roof level. On any normal project this would be a complex exercise, however with the additional environmental aspirations of 90 Long Acre requiring both blue and living roofs to be installed, this complexity was significantly magnified. To achieve success a number of up-front planning and design workshops were organised, not just covering theoretical calculations but also discussing on-site practicalities and specific measurements of existing areas.
To meet the required thermal performance requirements on this project a weighted U-value calculation was required. However, we needed to ensure that enough weight was installed to avoid issues relating to flotation and wind uplift, and sufficient soil depth was also required to ensure that the living roofs could survive during different temperature variants.
Other design considerations included:
• Waterproofing system review, to determine which system was best suited to specific roof areas, as the project would require us to use a multitude of systems.
• Site measurement of existing upstands heights, deck preparation
• Drainage calculations and reviewed falls requirements in line with BS6229-2018
• Broof (t4) fire safety system requirements
• Environmental standards & benefits
• BIM design
• Buoyancy
Environmental product performance was a key priority on this project and the revised roofing and cladding systems put forward by MAC offered many additional benefits compared to the original specification. At the initial design stage we reviewed the BREEAM requirements and assessed the ‘Cradle to Cradle’ performance of each system. This included information on where the materials were coming from, whether they could be sourced locally to reduce carbon impact, and whether all materials were being responsibly sourced. All products that we installed also had all required certification.
During our pre construction phase and part of our technical submittals, we ensured waterproofing systems put forward had all relevant environmental declaration of performances including EPD information where available, as part of overall technical submittal.
Material waste was kept to a minimum, for example, if it was not able to be disposed of through the allocated waste skips on site, it was removed by our own waste carrier with all waste notes being submitted to demonstrate that it had been disposed of in the correct way and in full compliance with our ISO 14001 process.
MAC are accredited to ISO 14064-1 (Net Carbon Zero) and ISO 14001 (Environmental Management) and are also part of the supply chain sustainability school. We were therefore able to accurately track and record our carbon emissions, waste, materials usage and energy consumption on this project through the use of BRE Smart Waste, which contributed to achieving the BREEAM outstanding targets of the project. As part of our on-going process of continuous improvement strategy, MAC are now implementing BRE Smart Waste into our daily business and, once fully operational, this will be used to track all projects that the business undertakes.
Green Roof Performance
The introduction of green and biodiverse roofs on this project were designed to create a desired habitat that will attract particular flora and fauna, whilst also contributing to enhanced mental health and wellbeing by offering natural green spaces, reducing urban heat islands, and improving air quality for local residents and building occupants.
The green roof installation included a special London Wildflower seed mix which contains 25 species to encourage Biodiversity. This mix was designed to mimic the natural plant life that occurs in the South East of England, specifically in the London area, within the sedum finish, providing a natural habitat for indigenous pollinators and other wildlife. This will help contribute towards increased biodiversity in the local urban environment, while reducing surface water runoff through rainwater retention, easing the burden on the drainage systems and reducing flood risk.
The specified green roof system also utilised recycled and recyclable materials, such as drainage boards and geotextiles, ensuring minimal construction waste. In addition it incorporated responsibly sourced materials, ensuring minimal ecological disruption during procurement.
As a refurbishment project, the sedum and biodiverse living roof system incorporates innovative materials such as lightweight drainage boards and substrate blends designed to optimise plant growth while reducing load on structural elements.
On Roof Level 9, the roof garden system was installed using a PV Wildflower seed mix that has been developed for use under photovoltaic panels. This seed mix contains 26 native species as a vegetation finish which have been carefully chosen to provide a long flowering season and low growth height from Spring to late Autumn, with a varied range of colour and habitat. This is attractive to pollinators and provides an aesthetic appearance, and when installed in conjunction with photovoltaic panels, this provides an extra benefit as the green roof vegetation beneath the PV panels helps to cool them down and make them more efficient.
All living roof finishes used on this project contributed towards both local Biodiversity Action Plans and BREEAM ecology credits.
Blue Roof Performance
On this project, the largest roof on Level 9 featured a specially patented blue roof rainwater attenuation system, manufactured by ACO. Whilst other systems involved storing the rainwater directly on top of (and in contact with) the roof waterproofing membrane, ACO’s system features a separate attenuation tank that sits on top of the roof. This means that the roof waterproofing is not under continual stress of hydrostatic pressure etc with water being continually sat on it. As a result the system helps derisk the building and extend the life of the waterproofing membrane, again lowering the overall environmental impact. Having the excess water stored separately away from the roofing membrane also avoids any potential problems arising from flotation of the insulation.
MAC worked in conjunction with ACO to visit the site and provide calculations for the water attenuation the building would need, and a solution was then recommended that could provide the attenuation required in line with the overall sustainability goals and planning conditions of the project.
The calculations made accounted for the different sections of roof and the fact that raised areas of the roof drained onto lower parts. They also took into consideration the combination of blue and blue green roof that was to be installed as part of the plan to better conserve water, boost biodiversity, clean the air, and improve the microclimate of the building.
Blue roof systems, such as the one used on this project, are designed to reduce the impact of surface water discharge and reduce potential downstream flooding. With a project such as 90 Long Acre, the only credible alternative within the footprint of the building would be to have a free-standing storage tank held below ground in a basement, and from here the water would almost certainly need to be pumped to the sewer. This would entail an extra ongoing environmental cost in terms of the energy required to pump the water stored below ground up into the sewer system. However with the blue roof system, the rainwater can be effectively stored at roof level before being discharged into the sewers in a controlled manner using gravity.
Social Value
MAC’s Social Value Team, headed up by our Social Value Manager (Sue Jones) ensured we met all of our social value obligations on this project. For example, we conducted a number of local school visits where we gave interview training and attended career fairs. We also carried out classroom talks across a number of schools on “What is my Job?” where a number of different MAC people attended to provide information on various careers available in the construction industry.
On this project we directly employed 2 trainee site operatives from the local area, and they were able to learn the basics and develop new skills, before progressing on to their NVQ in roofing.
Our Procurement Team invited local suppliers to tender for works on this project, not only to keep local spend local but also to reduce the environmental impact arising from transportation to and from site. An important part of this process was to ensure that local suppliers not only secured orders for this project, but that they continued to sustain income once the works had been completed. To achieve this our Procurement Team ensured that these suppliers were approved as part of MAC’s approved supply chain, which will mean that they are given opportunities to secure orders on future projects elsewhere.
From a practical point of view, the design of the new 90 Long Acre building incorporates a large amount of outdoor amenity spaces for residents to enjoy. This is a positive, multi-functional use of the roof areas, helping to contribute towards general health and well-being of the residents.
Health & Safety
From the start of our involvement in this project right through to completion, our thought process was always how do we deliver this project in a smarter, greener, quicker and safer way. As such MAC’s Project Team constantly reviewed these objectives and worked closely with the Main Contractor to achieve them as they shared the same mind-set as ourselves.
Throughout the design process we worked with the manufacturer’s Technical Team, the Client’s Team and the Main Contractor’s Team to ensure all best possible methods were being captured and used, delivering a safer, greener and smarter mode of working.
MAC’s HSEQ Team worked with the Client’s HSEQ appointed person to deliver a presentation that outlined the HSEQ requirements of this project, highlighting any project specific needs to our Installation and Project Teams. This procedure forms part of our company’s strict operating standards in line with our ISO accreditations – 9001/14001/45001/14064-1.
As part of our site supervision we also carried out “Safe2Start & Safe2Finish” talks and inspections each day, which were also adopted by other sub-contractors working on this project, as they saw it as good practice and we were happy to share our process with them.
MAC ensured that our HSEQ Manager carried out regular HSEQ inspections in line with the project requirements to ensure we were meeting all KPIs for this project:- indeed this project was actually audited as part of our recertification for our ISO accreditations.
Complex Detailing
To the higher-level roof areas where the blue roof system was being installed there were more than 100 penetrations that had to be waterproofed, and detailed using a pitch pocket detail to each penetration. These penetrations were there to support M&E equipment, Solar panels and plant screening situated on the roof areas.
As part of the installation process, each individual component that formed the waterproofing and blue roof system had to be tailored to size, on site. This meant cutting the insulation, ACO RoofBloxx and pavers to size so that that they fitted tightly around each penetration.
To demonstrate this, MAC created a sample rig on site to demonstrate the sequencing of this installation. We did this live in time with the material supplier’s technical team working in collaboration with ours, so that the architect and client could see. This helped to further demonstrate the quality of installation that they would be getting from ourselves, and promoted the positive collaboration and culture between all parties, which was a key objective for everyone involved with this project.
The pitch pocket detailing was very labour intensive, but this was a critical waterproofing detail to get right. MAC’s experienced on-site operatives installed these pitch pockets with great accuracy, quality and in accordance with the manufacturer’s installation details. This was then signed off their site services team as part of their QA and guarantee process, which in turn formed part of an overall digital QA document. We produced this using Field View – View point, and it then became part of our O&M manual.
There was also complex detailing required to the existing gutter areas. This was primarily around the higher level lead areas, where the plan was to keep as much of the current lead roofing in place and make it fit for purpose, thereby contributing further towards sustainability targets. This detailing this was largely achieved however some of the gutter areas had come to end of their life cycle in this application, with numerous repairs already carried out during this period. As these gutters could not be seen, it was agreed that it would make sense to install a cold applied liquid (lead grey) to these areas instead, as this would make the installation safer, whilst the intricate detailing would be made easier and the waterproofing would form part of the overall guarantee that was being offered. Wherever possible, any materials that we removed were then repurposed for use as lead flashings in other areas of the project.
The porcelain pavers were one of the main features visual features to the terrace areas, and the installation of these paver required incredible attention to detail. It was essential to ensure that all pavers aligned perfectly, that all cuts and patterns matched, and that we achieved the architectural finish that was required by the client.
Project Team:
MAC put together an experienced Project Team that would deliver these works from start to finish. All members of the Team committed to understanding the project inside and out before it started, buying in to all requirements and KPIs. A dedicated Project Team organigram was put together and submitted to the Client including all relevant company CVs. We also arranged a “meet and greet’ for the various Project Teams on site, so that each Project Team could meet their opposite number before the project started.
So that MAC’s Team could better understand the project we arranged for the Main Contractor to give us an overview of the project and its requirements. This was not only limited to our works but also included other trades as well, as this gave us the opportunity to learn what their key objectives were and what requirements we all needed to achieve to support the areas we were working in. This meeting also gave us the opportunity to demonstrate how we would support and meet these requirements.
Before the project started, MAC’s Operational & Planning Team attended a number of workshops to develop a programme that met all key milestones, including design, procurement and labour requirements. To meet the peak requirements of the project, this programme was updated weekly in conjunction with the Client to ensure we all remained on target for our agreed completion date.
At the start of this major project MAC held installation workshops with our Project Management and Installation Teams. In these workshops we went through key factors such as:
• What the project entailed
• Its requirements
• Sequencing of works
• Interfacing
• System build ups
• Workmanship
All design details and system build ups were then uploaded to our BIM 360 platform which was available to all members of the Project Team and Installation Team. This platform is also available to our Teams via their I-Pads which allows them to refer to details and system builds quickly and efficiently whilst on site.
It is MAC’s strong belief that our things shouldn’t be left to chance, and we insist on checking and reviewing things before checking them again. We endeavour to design out issues during our pre-construction and design phases, so that the only issues we encounter are sporadic. Where these issues do arise, we engage with our supply chain partner’s Technical Team and our own in-house Technical Team to come up with a robust solution. This is then drawn up into a 2D or 3D drawing which is submitted for approval by our client before we proceed.
MAC worked closely with the onsite Technical Services Teams to ensure that they were carrying out regular site checks and producing reports on our installed works. This was carried out on a 2-week cycle, whilst further checks were also caried out by our in-house Technical Services Manager. His sole job function is to check our installed works throughout the installation period against the manufacturer’s laying instructions and against our own approved drawings to ensure that when we hand over these finished roof areas, they are defect-free. All flat roofing areas were also electronically tested as part of our strict QA process, whilst all site documentation and QA is recorded through Field View – View point, a cloud-based system which is operated via tablets to avoid paper wastage.
- Gallery
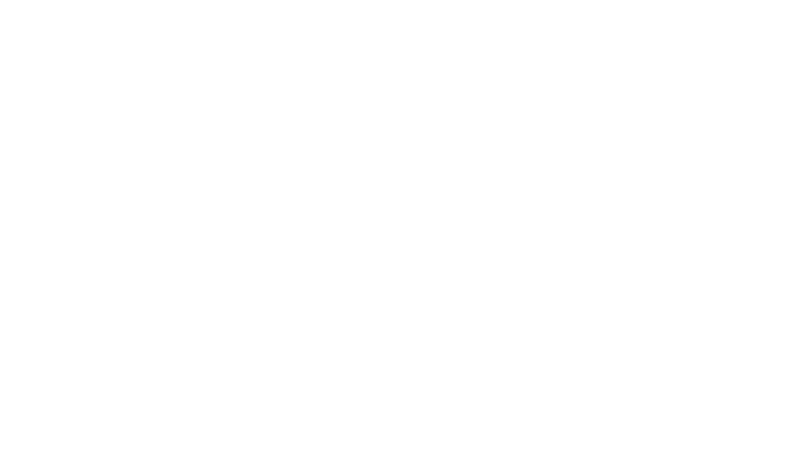
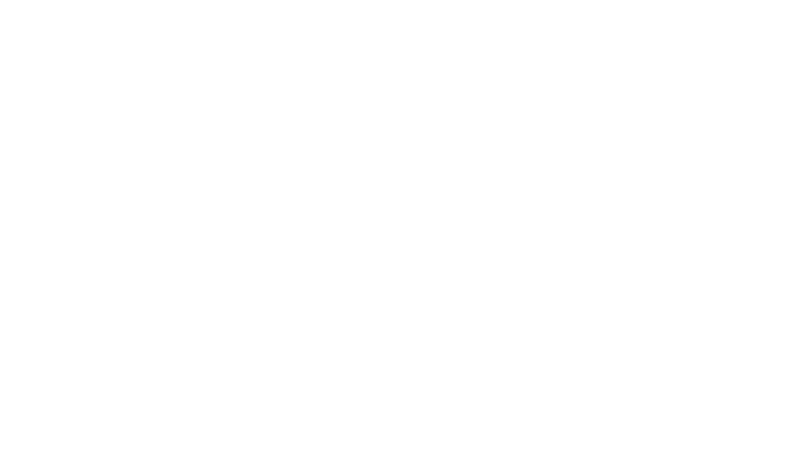
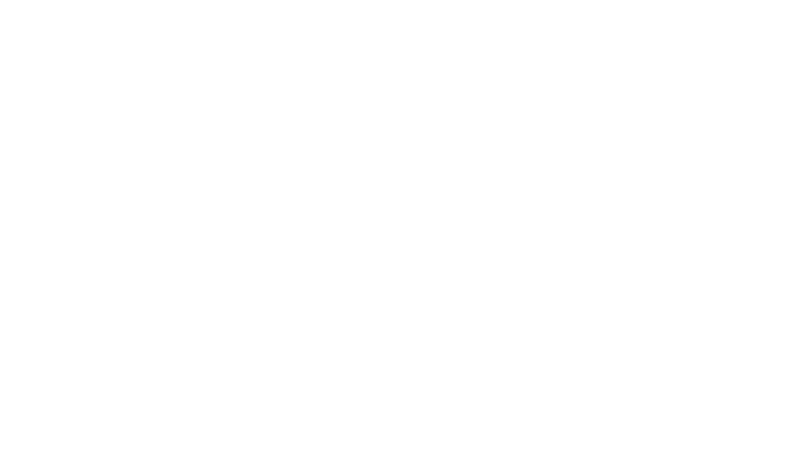
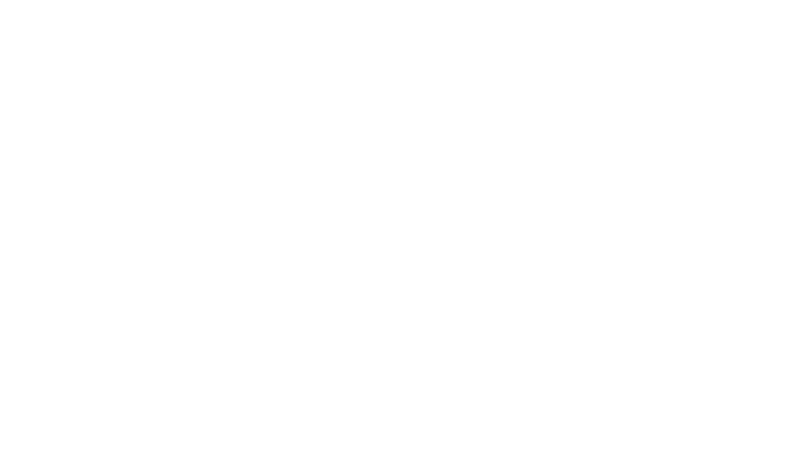
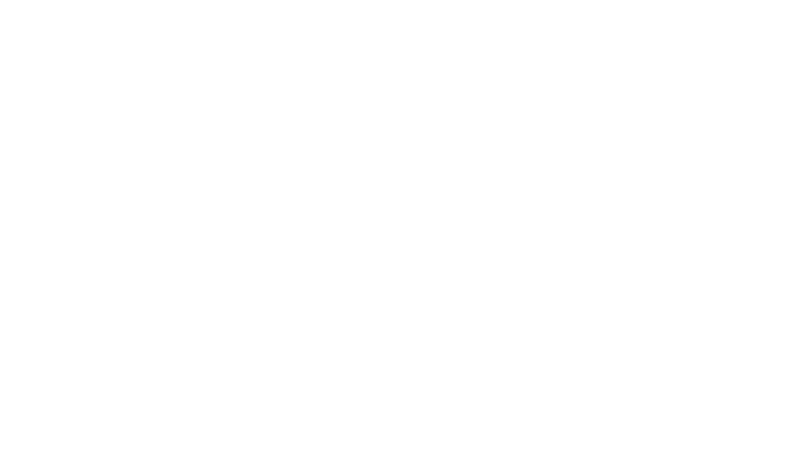